Needle valves are an essential component of many industries, from laboratories to medical equipment. These valves allow for precise control over gas and liquid flows, making them a popular choice for applications that require accuracy and reliability. In this blog, we will take a closer look at needle valves, their working principle, and their various applications in industrial settings. We will also discuss the advantages of using needle valves over other types of valves and factors to consider when selecting the right needle valve for your needs. So whether you’re an engineer or a technician, read on to discover why needle valves are a must-have in your toolkit.
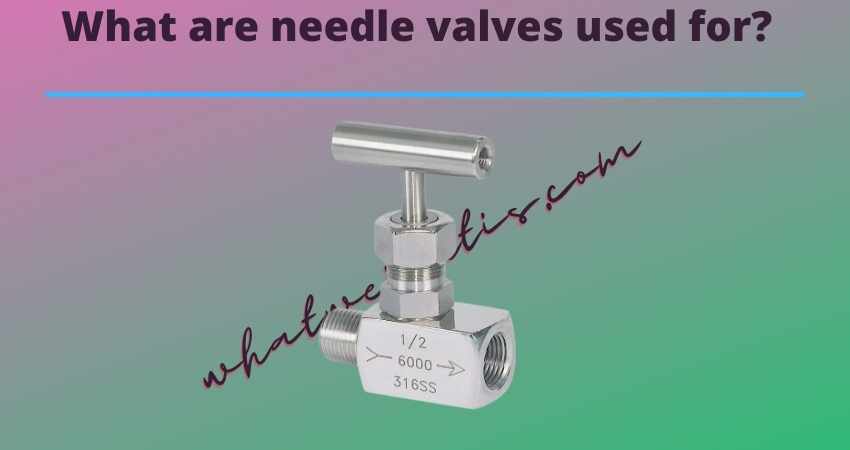
Introduction
Needle valves are a type of valve that provides precise regulation and control of fluid flow and pressure. They use a sharp, needle-shaped disk to control the flow rate. Needle valves can be operated manually or automatically using hydraulic motors or air actuators to adjust the plunger’s position based on external data. The needles and seats in these valves are designed to fit together precisely, allowing for fine control of flow by depressing or retracting the needle. Needle valves have a small orifice with a long, tapered seat, and a needle-shaped plunger on the end of a screw that can impede fluid flow until the plunger is completely retracted. These valves are commonly constructed using stainless steel due to its strength and durability. Overall, needle valves are essential components in various industries where precision flow control is needed.
Understanding Needle Valves
Needle valves are regulating valves that allow engineers to finely control and regulate fluid flow and pressure with a threaded needle-shaped plunger. They’re used in a range of applications across various industries, including controlling or metering steam, air, gas, oil, water or other non-viscous liquids. Needle valves play a critical role in the safe and efficient operation of machinery in industrial settings by measuring and controlling flow with exceptional accuracy. Installing instrument needle valves can save time and money by isolating pressure instruments for safe and convenient installation. Needle valves can operate manually or automatically, with automated valves being connected to a hydraulic motor or an air actuator that adjusts the plunger’s position according to timers or external performance data. Overall, needle valves are reliable precision tools essential to many operations that require careful control over fluid flow and pressure.
Definition of a Needle Valve
Needle valves are a type of valve used to regulate flow with high precision, making them ideal for applications that require constant, low flow rates. A needle valve uses a threaded, needle-shaped plunger to control the flow of liquid or gas through the valve’s channel, with the needle acting as a conical-shaped plunger. The needle and seat work together to ensure accurate and precise control of flow.
Needle valves are commonly used in flow-metering applications that require constant, low flow rates, such as in carburetor idle fuel flow. They are also ideal for instrument systems that require throttling of small volumes, as they can precisely control pressure and flow. Additionally, needle valves have metal to metal seats and are used where accurate flow control is essential, especially in situations where small rates of flow are necessary to prevent damage to delicate gauges. Overall, needle valves provide precise control and accuracy in low-flow applications.
Working Principle of Needle Valve
Needle valves are commonly used in industries where precise flow measurement is required, such as in the oil and gas, chemical, and pharmaceutical industries. They can handle more differential pressure than diaphragm valves and have two basic functions: isolation and regulation. A needle valve can turn the flow on or off and regulate the rate of flow through a system.
The working principle of a needle valve is based on a small port and a threaded, needle-shaped plunger that allows for precise regulation of flow, making them ideal for low flow rates. There are three types of needle valves available in the market: manually operated threaded needle valves, motorized needle valves that use electric or pneumatic actuators, and angle needle valves that turn the output by 90 degrees instead of in-line.
A tapered pin gradually opens a space for fine control of flow, and the flow can be controlled and regulated with the use of a spindle. Overall, understanding the working principle of a needle valve is essential to properly utilizing this tool for precise control over fluid systems.
Applications of Needle Valves
Needle valves are precision control valves that find application in various industries, including power generation, zoological sciences, cooling, instrumentation control, and gas and liquid dispensation. They are used for the precise flow control and metering of steam, air, gas, oil, water, and other non-viscous liquids. Needle valves can handle a high differential pressure compared to diaphragm valves. Motorized needle valves use an electric or pneumatic actuator to connect to and turn the plunger. Angle needle valves turn the flow from the inlet by 90 degrees for better system integration. Needles valves also serve as gas flow control valves in vacuum systems or shut-off valves for pressure gauges. However, slurries and viscous media can block the small orifice of a needle valve making it unsuitable for such applications.
Laboratory and Industrial Settings
Needle valves are widely used in numerous industries for their ability to control fluid flow and pressure with exceptional accuracy. They have a variety of applications, including laboratory and industrial settings. In laboratory settings, needle valves are typically used for precision control of small flows in analytical instrumentation. In industrial settings, they are often used to isolate pressure instruments for safe and convenient installation.
The major components of a needle valve include the body, needle/needle tip, gland packing, bonnet, and handle. Stainless steel is a commonly used material for needle valves due to its ability to withstand high pressures of up to 10,000 PSI. Needle valves are available with different connections, including NPT and BSPP threaded ends. Overall, the versatility and precision of needle valves make them an essential component in a wide variety of applications.
Gas and Liquid Control Systems
Needle valves are a versatile component used in various industries for precise control or metering of steam, gas, oil and other non-viscous liquids. They are commonly used to control gas flow rates and have low flow rates with significant pressure drops. Needle valves are especially useful in gas and liquid control systems where gradual and precise control over the amount of fluid passing through the valve is required to prevent damage to gauges and enable better regulation.
Motorized needle valves allow for remote and accurate control of flow rates in closed loop systems, while manual needle valves offer gradual and precise control over the amount of liquid or gas passing through the valve. Automated needle valves also provide this accuracy along with added convenience. Angle needle valves are a variant that turn flow by 90 degrees, allowing for better system integration. With their ability to provide reliable and precise flow control, needle valves are an essential component in various applications in many different industries.
Medical Equipment and Devices
Needle valves are critical components in various applications, including medical equipment and devices. Their precise control and regulation of fluid flow make them ideal for use in these settings. Motorized needle valves, which use electric or pneumatic actuators for remote control and accurate flow rate, are particularly useful in medical devices where precision is crucial.
Angle needle valves are another variation that offers better system integration as they turn the flow at a 90-degree angle instead of a straight line. Needle valves are also often used to isolate pressure instruments for safe installation without shutting down a process.
In medical equipment and devices, the symbol for a needle valve is represented by a standard 2-way valve symbol with an arrow indicating it is a needle valve. Overall, needle valves help ensure the safety and accuracy of fluid management in medical settings.
Advantages of Using Needle Valves
Needle valves are a type of valve designed to regulate the flow and pressure of fluids with precision, making them ideal for applications that require exact measurements. These valves are popular due to their ability to adjust flow rates in small increments, allowing for fine-tuning of processes. Stainless steel is a commonly used material for needle valves because of its resistance to corrosion.
Needle valves can be operated manually or automatically, with automated valves adjusting the plunger’s position based on external data. They are widely used in vacuum systems to release a controlled and steady supply of gas without high pressure. Three types of needle valves – manually operated threaded, motorized, and angle – are available in the market, each having its own advantages.
Overall, the main advantage of using needle valves is their precise control over fluid flow and pressure. Their versatility and range of applications make them an essential component in many industries, including oil and gas, chemical processing, and pharmaceuticals.
Precise Flow Control
There are several advantages to using needle valves for precise flow control. Needle valves are small in size, manually operated, and can control pressure and fluid flow with exceptional accuracy. This makes them ideal for regulating the flow of liquids, fluids, or gases at low flow rates.
The tapered pin of a needle valve gradually opens a space to achieve fine flow control. This allows for precise adjustment of the flow rate, making them highly useful in applications where accuracy is critical. Additionally, needle valves can also isolate pressure instruments for their safe and convenient installation and control pressure spikes during valve opening.
One common use of needle valves is to control gas flow, such as propane in a tank. Overall, the precise nature of needle valves makes them an excellent choice for any application that requires accurate and reliable flow control.
Low Leakage Rate
Needle valves offer several advantages that make them a popular choice in applications that require precise regulation of flow rates. One of these advantages is their low leakage rate, which ensures that gas does not escape from the valve when it is closed. This makes needle valves ideal for use in systems where even small leaks can cause problems.
In addition to their low leakage rate, needle valves have a small orifice and a tapered plunger, allowing for gradual and precise control of flow. Despite their low flow rates, needle valves can be used to release a controlled and steady supply of gas in vacuum systems. They can also function as reliable shut-off valves and can be motorized for automation.
When selecting a needle valve, it is important to consider factors such as pressure, size, temperature, and materials. By choosing the right valve for your application, you can ensure optimal performance and reliability.
High Pressure and Temperature Resistance
One of the main advantages of using needle valves is their ability to withstand high pressures and temperatures. Needle valves made of steel or stainless steel can handle pressures up to 10,000 PSI, making them suitable for a variety of industrial applications. While plastic needle valves are suitable for adjusting pure and corrosive fluids, they are not recommended for use in applications with high temperatures or pressures above 60 degrees Celsius.
Stainless steel needle valves, on the other hand, are resistant to heat and chemically aggressive media like seawater, making them suitable for high-pressure and temperature applications. They are also highly durable and have excellent overall chemical resistance to almost any media, except continuous exposure to saltwater which can lead to corrosion. Additionally, needle valves typically have NPT and BSPP threaded ends which make them easily connectable for fluid flow control applications.
Factors to Consider in Needle Valve Selection
Needle valves are an essential component in many industries, including oil and gas, chemical processing, and instrumentation. When selecting a needle valve for your application, several factors must be considered. First is the material of construction, which should be chosen based on the application’s specific needs. The port and orifice size should also be taken into account to ensure proper flow control. Additionally, the type of fluid and its pressure should be considered when selecting a needle valve.
The needle valve’s size should be chosen based on the expected flow rate and pipe size. Lastly, temperature is an important factor that must not be overlooked. The material used in the valve should be able to handle the range of temperatures it will encounter to prevent damage or failure. By carefully considering these factors during selection, you can ensure that your needle valve will perform optimally and provide reliable control over your fluid system.
Material of Construction
When selecting a needle valve, one important factor to consider is the material of construction. Common materials for the housing of needle valves include brass and stainless steel due to their chemical resistance. However, other materials may be used for special applications. The body of a needle valve can be made of brass, bronze, stainless steel, or other alloy materials. Valve seats may be made of PVC, CPVC, plastic, PTFE, or thermoplastic.
The stem of a needle valve allows for micrometer-like adjustment and comes in three configurations: simple screw-down, oblique angle, and controlled outlet flow. Additionally, needle valves can have metal to metal, plastic to plastic, or plastic to metal seats and needles, allowing for a range of materials to be used in their construction. Overall, understanding the material options available for needle valves is an important consideration when selecting the right valve for your specific application.
Fluid Pressure and Temperature
When selecting a needle valve, there are several key factors to consider. Material, pressure, size, and temperature all play a role in determining which valve is best for your specific application. The material of the valve should be chosen based on the type of fluid being controlled and any potential corrosive properties it may have.
The fluid pressure rating of a needle valve should also be carefully considered during selection. Proper sizing is crucial for optimal performance and ensuring that the valve can handle the required flow rate. Additionally, the temperature of the fluid being controlled needs to be taken into account as this can affect the performance of the valve.
Overall, it’s important to carefully consider all factors when selecting a needle valve to ensure that it will meet your application’s requirements and provide reliable and consistent operation.
Orifice and Port Size
When selecting a needle valve, it’s important to consider several factors to ensure proper function and performance. One of the most important considerations is the orifice and port size, which typically ranges from 2 to 12 mm or 1/8” to 2”. The tapered pin of the needle valve allows for precise flow control, making it ideal for low flow rates and fine regulation.
In addition to orifice and port size, other key factors in selecting a needle valve include valve material, temperature and pressure rating, size, and connection ports. Connection ports can be male or female with NPT, BSP, and metric thread standards commonly used.
Proper selection of the correct port and orifice size in needle valves can promote effective flow and system performance while reducing wear and/or leakage. Taking all these factors into consideration can help ensure you choose a needle valve that best meets your specific needs.
Needle Valves vs Other Valves
Needle valves are a type of valve that is commonly used in fluid throttling applications or for isolating an instrument from a process. Unlike other valves, needle valves have a needle-shaped plunger that precisely regulates the flow of fluids. Stainless steel needle valves are widely used in high-pressure applications due to their durability and resistance to corrosion.
When comparing needle valves to other types of valves, there are several key differences to consider. Gauge valves, for instance, mainly separate a process from instrumentation, while needle valves are specifically designed for fluid throttling applications. Additionally, gate valves have a flat gate that moves up and down to control the flow, whereas needle valves use a pointed stem.
Needle valves also have a distinct symbol on engineering drawings, making them easy to identify. When choosing between different types of valves, it’s important to consider factors such as pressure rating, flow control requirements, and compatibility with the fluid being used.
Needle Valve vs Globe Valve
While both needle valves and globe valves are used for fluid control, there are some key differences between the two. Globe valves have a spherical body that allows for full shutoff when needed, but they can be more difficult to operate and require more maintenance than needle valves.
Needle valves, on the other hand, have a needle-shaped plunger that provides precise control over fluid flow. They are often used in high-pressure applications due to their ability to handle high pressures and resist corrosion.
When choosing between a needle valve and a globe valve, it’s important to consider factors such as fluid pressure and flow control requirements. Needle valves are typically better suited for applications that require precise flow control and high pressure resistance, while globe valves are better suited for applications that require full shutoff capability. Ultimately, the choice between these two types of valves will depend on the specific needs of your application.
Needle Valve vs Ball Valve
Another type of valve often compared to needle valves is ball valves. The main difference between the two is that ball valves use a spherical disc to control the flow, whereas needle valves use a pointed stem. Ball valves are popular for their ease of operation and ability to quickly open or close the flow, while needle valves are preferred for their precise flow control and high-pressure resistance.
When choosing between a needle valve and a ball valve, consider factors such as the required level of fluid control, pressure rating, and compatibility with the fluid being used. Needle valves are typically better suited for applications that require precise flow control and high-pressure resistance, while ball valves are more suited for applications that require quick shutoff and low maintenance. Ultimately, your choice will depend on the specific needs of your application and the type of fluid being used.
How does a plug valve work?
Conclusion
In conclusion, needle valves are a crucial component in various industries that require precise flow control and reliable fluid regulation. They offer advantages such as low leakage rate, high pressure and temperature resistance, and precise flow control. It is essential to consider factors such as material of construction, fluid pressure and temperature, and orifice and port size when selecting the right needle valve for your application. While there are other types of valves available, needle valves stand out due to their ability to provide accurate flow control in a vast range of applications. To learn more about needle valves and other valve options for your industry needs, contact us today.

Mr. Jasim Uddin holds significant knowledge, skills, and experience in several fields relating to electrical engineerings, such as power electronics, telecommunications, and data transmission. The articles on engineering are very interesting to him, and this is why he finds writing engineering articles to be very fun.