Have you ever wondered what valves are and why they are used? Did you know that check valves are valves with a specific function? If so, then you’re in the right place! In this blog, we’ll be telling you everything you need to know about check valves. We’ll tell you about their different types, applications, and how to operate them. Ready to learn all about check valves? Let’s get started!
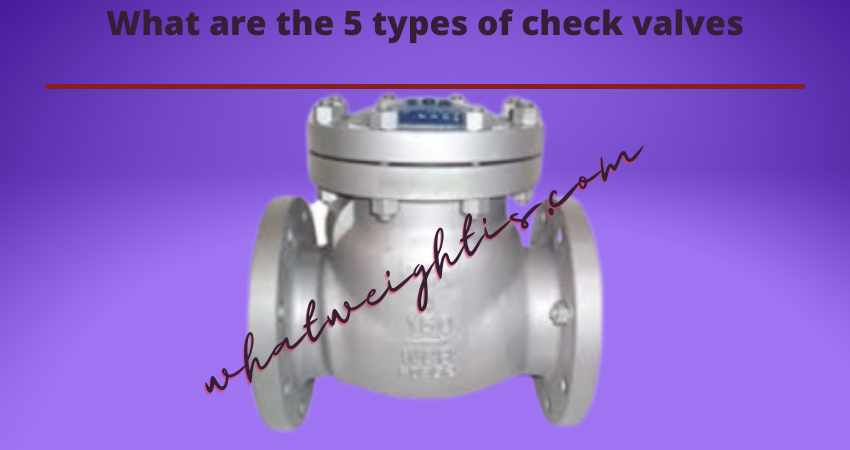
Overview of Check Valves
Check valves are used in the oil and gas industry to prevent backflow of fluid and maintain pressure in piping systems. There are a variety of types of check valves, such as in-line check valves, excess flow check valves, and aircraft check valves.
In-line check valves are used in applications where backflow of fluid is not necessary, such as pump and compressor discharge. These check valves are designed to withstand high pressure waves and other types of severe stress on the piping system.
Excess flow check valves are designed to stop flow of fluid when the pressure is greater than the check valve setting. These check valves can be used in applications where backflow of fluid is not needed, such as heat exchangers and reactors.
Aircraft check valves are used in applications where backflow of fluid is needed, such as watertight aircraft cockpits or water-intake systems for jet engines. These check valves are designed to provide watertight seals against high-pressure water flow.
Check valves are used in various industries such as offshore oil & gas production, onshore oil & gas production, gas plants, and liquid gases. They’re designed to withstand high pressure waves and other types of severe stress on the piping system.
Different Types of Check Valves
Check valves are valves that regulate flow in a piping system. They’re used to prevent back flow of water, among other functions. There are many types of check valves, with each type offering a different function and design.
– Swing check valves open when the flow is greater than the valve’s capacity, and they close when the flow is less than the valve’s capacity. They’re commonly found in water systems and industrial applications.
– Lift check valves (also known as piston check valves) open when pressure in the piping system is greater than the valve’s lift, and they close when pressure in the piping system is less than the valve’s lift. These check valves are also commonly found in water systems and industrial applications.
– Wafer check valves feature two circular disc-shaped interlocking pieces. When opened, water flow through a pipe can be blocked by moving one of the pieces upward. This check valve is commonly used in wastewater systems.
– Stop check valves are simple types of closed-face check valves that stop water flow once they’ve been fully opened or closed. They’re commonly used in water systems and industrial applications.
– Tilting-disk check valves consist of a disk with two detachable parts that can be tilted to block water flow or allow it to pass through a pipe. This type of check valve is commonly used in water systems and industrial applications.
Lift Check Valve
Lift check valves are valves that are used to control and regulate flow in a pipeline. They are typically used in applications where high flow rates or pressures are needed and can be sensitive to backflow. These check valves typically consist of a disc-shaped valve body mounted on a piston-like body connected by a flexible shaft to an inlet or outlet. The disc of the valve lifts up from the valve seat to allow flow, while closing against the reverse flow of fluid. When pressure in the pipeline is low, the valve will open freely, allowing any wastewater to flow through it without causing backflow. However, when pressure in the pipeline exceeds a certain level (typically 10–15% of the pipeline’s rated pressure), lift check valves will automatically close and stop flow. This is done by using a spring-loaded disc that lifts off of its seat when pressures reach significant levels.
Piston Check Valve
Piston check valves are types of check valves that are used in flow control in piping systems. These valves operate by controlling the flow of fluid in a piping system with a linear motion piston. These check valves require a minimum upstream pressure (pressure differential between inlet and outlet) to open the valve and allow fluid flow. The flow of the valve is controlled by the pressure passing through the pipeline or system. When normal flow occurs, the piston valve’s weight positions it in the closed position and prevents backflow of fluid into the pipeline. However, when reverse flow occurs, gravity causes the piston valve’s weight to drop into the open position, allowing backflow of fluid from the pipeline and closing off any flow.
Ball Check Valve
Ball check valves are a type of check valve that uses a ball-shaped valve to create a seal in flow systems. They are most commonly used in high-pressure flow systems such as water, gas, and steam systems. These check valves use a ball that closes when pressure in the system exceeds the cracking pressure of the ball. The ball check valve can be configured in several different ways to suit different applications and needs. For instance, some ball check valves have an external check ball that fails when the internal ball closes. Others have a spring-loaded spherical ball that closes against an internal seat. In some types of ball check valves, both types of ball can be present at the same time. To ensure positive closure of the orifice, the sealing seat of these valves is conically tapered to guide both balls into place.
True union ball check valves allow for easy removal and replacement of balls, making them ideal for applications where replaceable components are available or desired. Ball check valves are often very small, simple, and cheap, making them an economical choice for applications where precision and leak-free operation are crucial. Overall, ball check valves provide reliable flow control in high-pressure flow systems and are an integral part of many industrial processes and systems.
Swing Check Valve
Swing check valves are check valves that consist of a disc that is mounted on a hinge. As the name suggests, the disc can swing open in response to the flow of water. This type of valve is commonly used in applications where reverse flow of water is not required frequently to avoid “valve chattering”. Swing check valves are often used in water supply and wastewater treatment systems. A replaceable composition washer may be fitted on the disc to take most of the wear and tear. The best place for swing check valves is usually in the horizontal position, but they can also be mounted vertically if there is enough space. These valves should always be installed so that their hinge faces up and away from any potential sources of contamination.
Top-hinged Check Valve
Top-hinged check valves have a disc that is attached to the inner top of the valve with a hinge for it to open and close. The disc of a top-hinged check valve can swing open and shut when inlet pressure increases or decreases. Top-hinged check valves are designed to close when there is backflow in the system, which is typically achieved by using springs to assist in closure. These valves are generally used in applications with less frequent reversal of flow, such as water supply systems and air-conditioning systems. The closure of top-hinged check valves is assisted by springs, allowing them to easily close when in operation. They are a popular choice for applications requiring quick, reliable closure of flow in plumbing systems.
Common Applications for Check Valves
Check valves are used in various industries, such as offshore oil and gas production, onshore oil and gas production, gas plants, liquefied natural gas (LNG), refineries, petrochemical plants, chemical plants, fertilizers, terminals, pipelines, power plants, desalination plants, water plants and safety systems. Check valves are used for regulating flow of gases or liquids in closed systems. They prevent reverse flow of fluid in the system due to pressure difference across the valve.
In case of check valves being used in high-temperature service applications or geothermal applications or high-pressure safety valves check valves are required to be of stainless steel material with a pressure rating of 4500 psi or more.
In shutdown cooling systems check valves are used to isolate the cooling water from the system when the utility power is turned off. Once the water is no longer flowing through the check valve check valves are no longer required in these types of systems.
Check valves also come in different types such as ball check valve, disc check valve and globe check valve depending on their applications and features.
This type of valve has advantages like easy operation, low cost and durability. Also they can withstand high pressure of fluid flow. However their disadvantage is that they could jam easily leading to a partial closure of flow path.
With so many types and applications you might wonder what type of check valve is ideal? Well ball check valves have been found to be optimum among types as they have good flow rate with minimal back pressure. Besides disc and globe check valves have different applications too depending on the requirement of flow rate desired. So keep reading and learn about different types of check valves as well as their applications in various industries <E
Frequently Asked Questions
What are the five types of check valves?
The five types of check valves are the Swing check valve, Lift check valve (piston and ball), Wafer check valve, Stop check valve, and Tilting-disk check valve.
Check valves are controlled by pressure and opening when there is more pressure coming in from the inlet, or closing when there is no inflow pressure.
When inlet pressure overcomes the cracking pressure of a butterfly or wafer check valve, the two sides of the valve open.
How are check valves used in plumbing systems?
Check valves are used in plumbing systems to prevent backflow and keep valves sealed in the system. Check valves are commonly used on centrifugal pumps to prevent water from flowing back into the system. In Offshore Oil & Gas Production, check valves are used to prevent water from blowing back out of the production well during drilling and when the system is being pressurized. Check valves are also used in Onshore Oil & Gas Production, Power, Desalination, and Water for a variety of reasons.
What are the benefits of using check valves?
Check valves are beneficial to a piping system because they help to prevent backflow and maintain pressure. This leads to increased energy savings and reduced maintenance costs. check valves are flexible when it comes to flow, meaning they can handle variations in pressure easily. Thus, they’re less likely to fail.
Check valves are also operated by pressure, which means that they will open when there is more pressure coming from the inlet. This prevents objects from being inflated without continuous air pressure and protects mechanical equipment in the piping system.
The Basics of how to Check Valves work: How to Make Sure They Work Properly
Conclusion
Check valves are essential in any fluid flow system. Their main function is to stop fluid flow in the direction of flow when the pressure in the system decreases, and vice versa. They ensure that fluid flow is directed only in one direction and not back or forth. They are used in water systems, sewage systems, pipeline systems, and more. You can learn more about check valves by reading up on different types of check valves and their applications.

Mr. Jasim Uddin holds significant knowledge, skills, and experience in several fields relating to electrical engineerings, such as power electronics, telecommunications, and data transmission. The articles on engineering are very interesting to him, and this is why he finds writing engineering articles to be very fun.